BreatheSafe News
Discover the latest technology in the industry
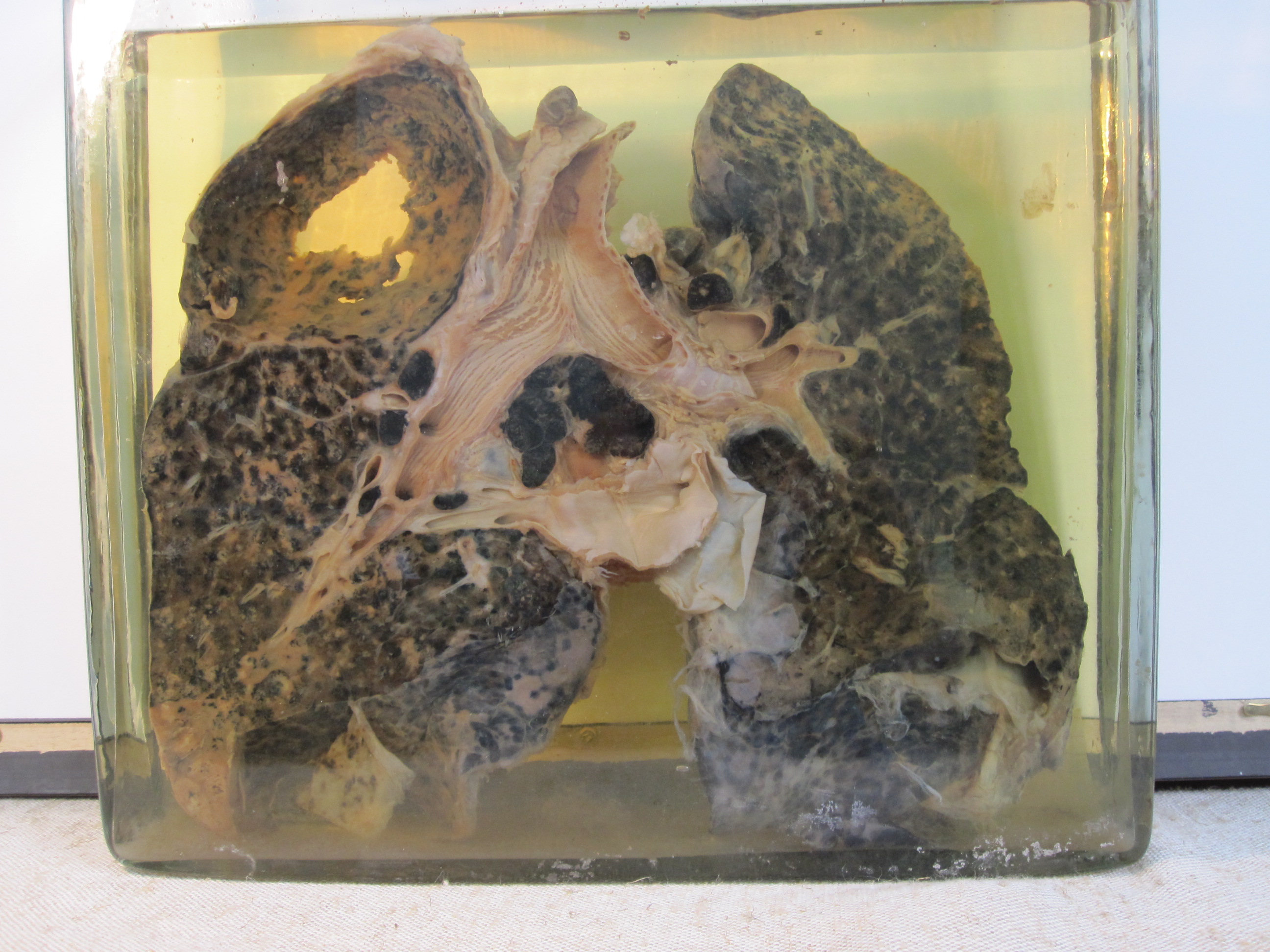
2025
12/06
Lung Diseases in Heavy Industries: COPD, Silicosis, and More
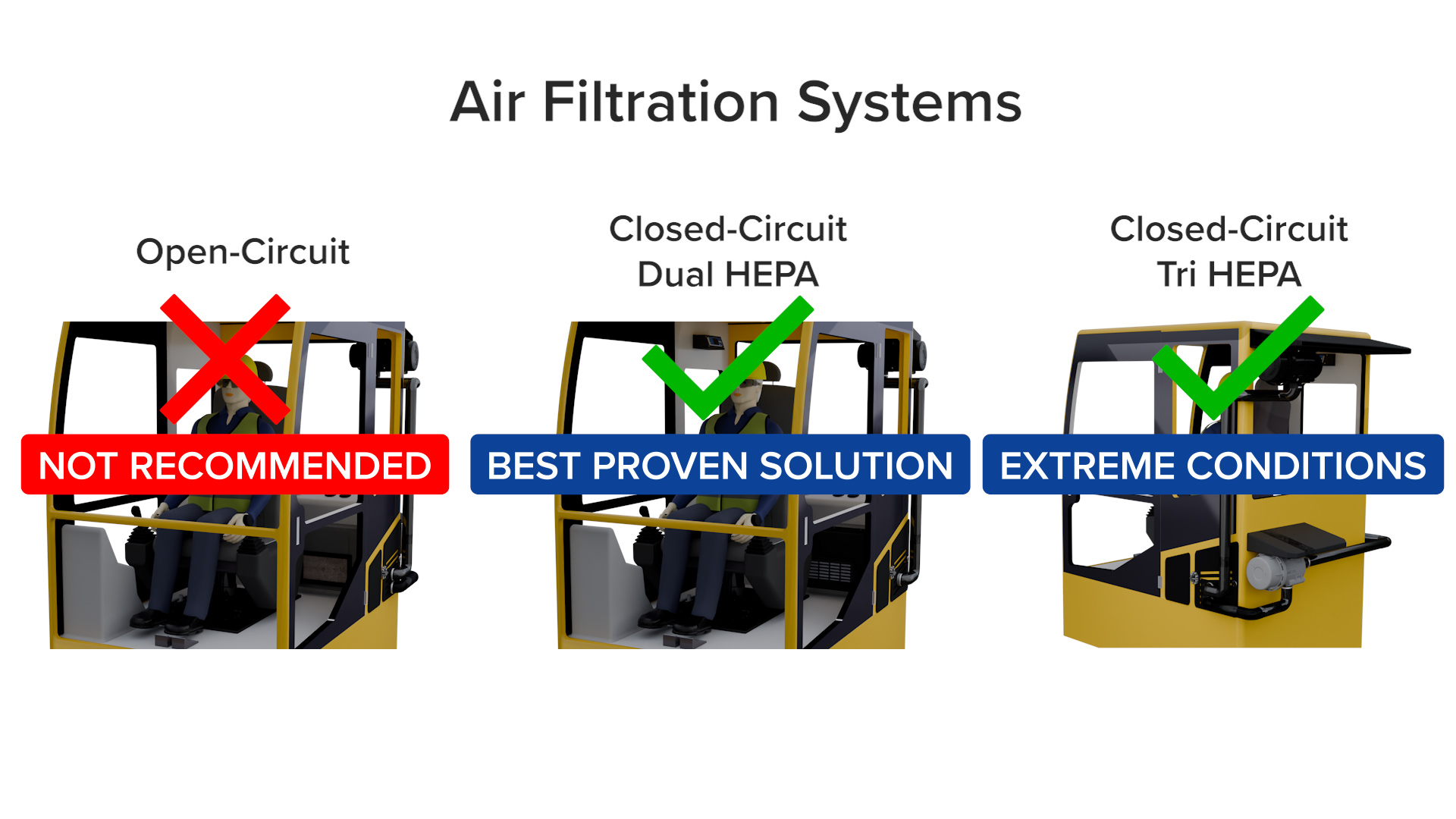
2025
07/04
Comparing Filtration Systems: What is the BEST?
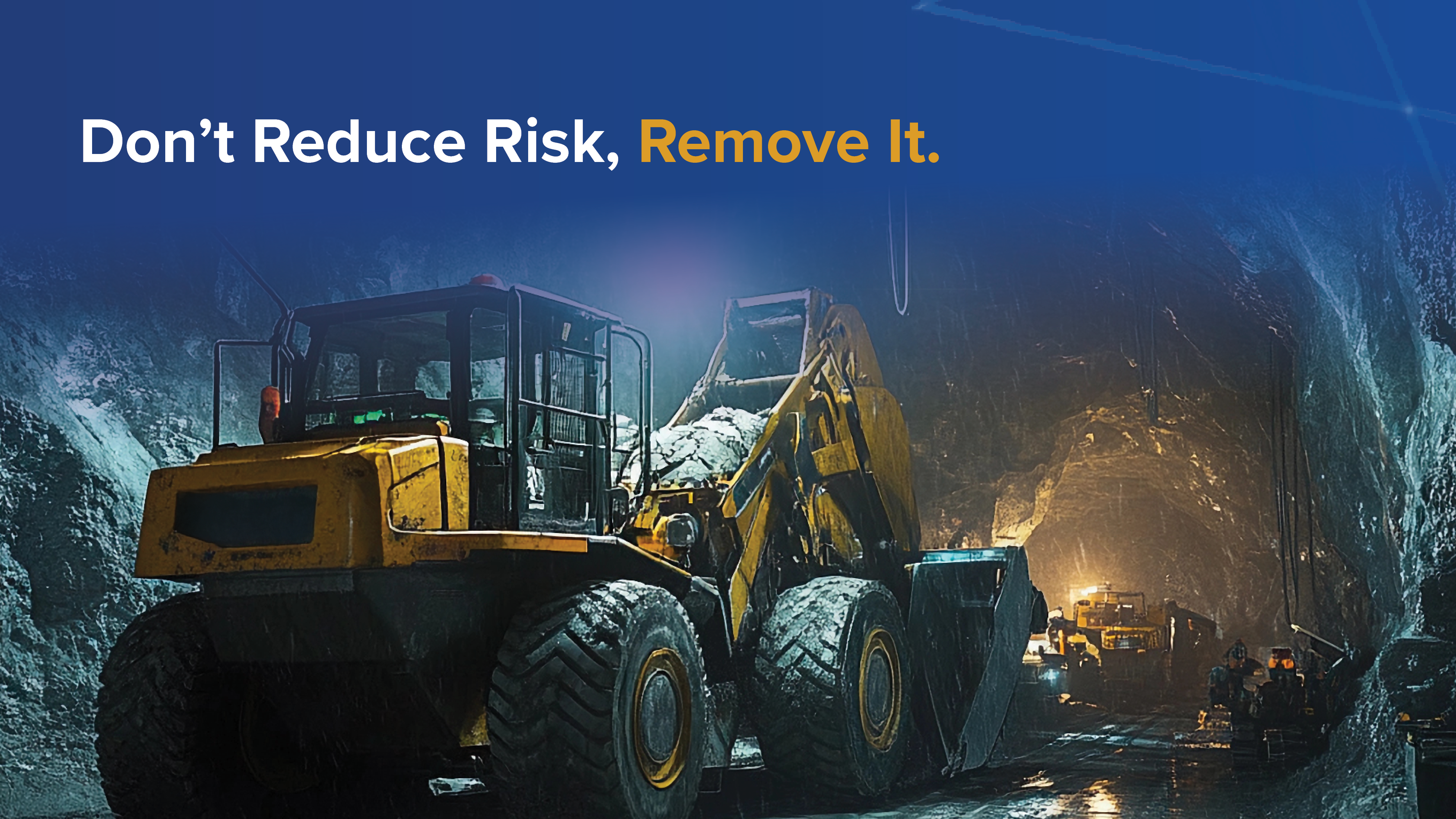
2025
07/04
BreatheSafe at the Underground Operators Conference
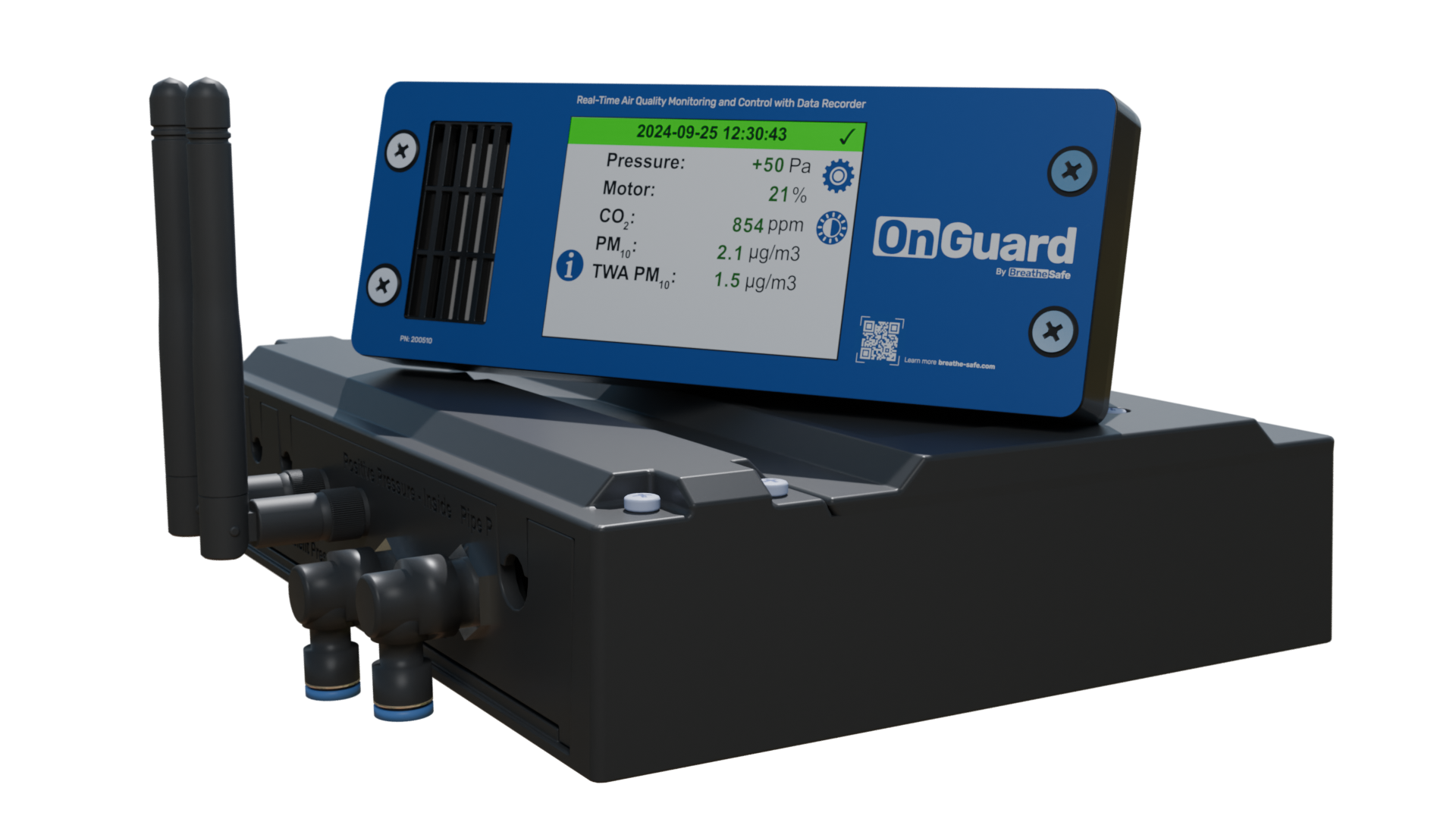
2024
11/09
Product Video – OnGuard Air Quality Manager
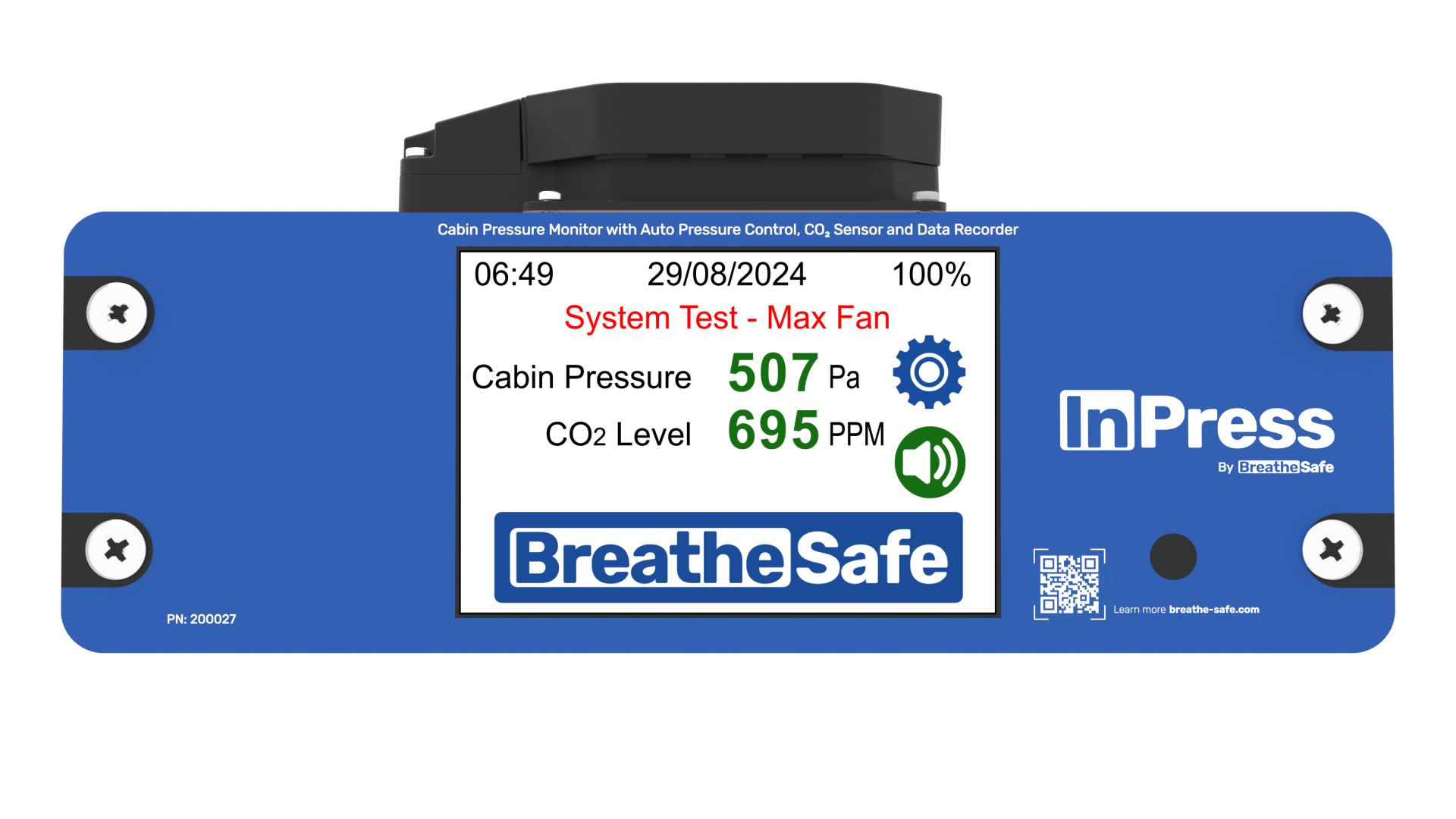
2024
11/09
Product Video – InPress Pressure Monitor
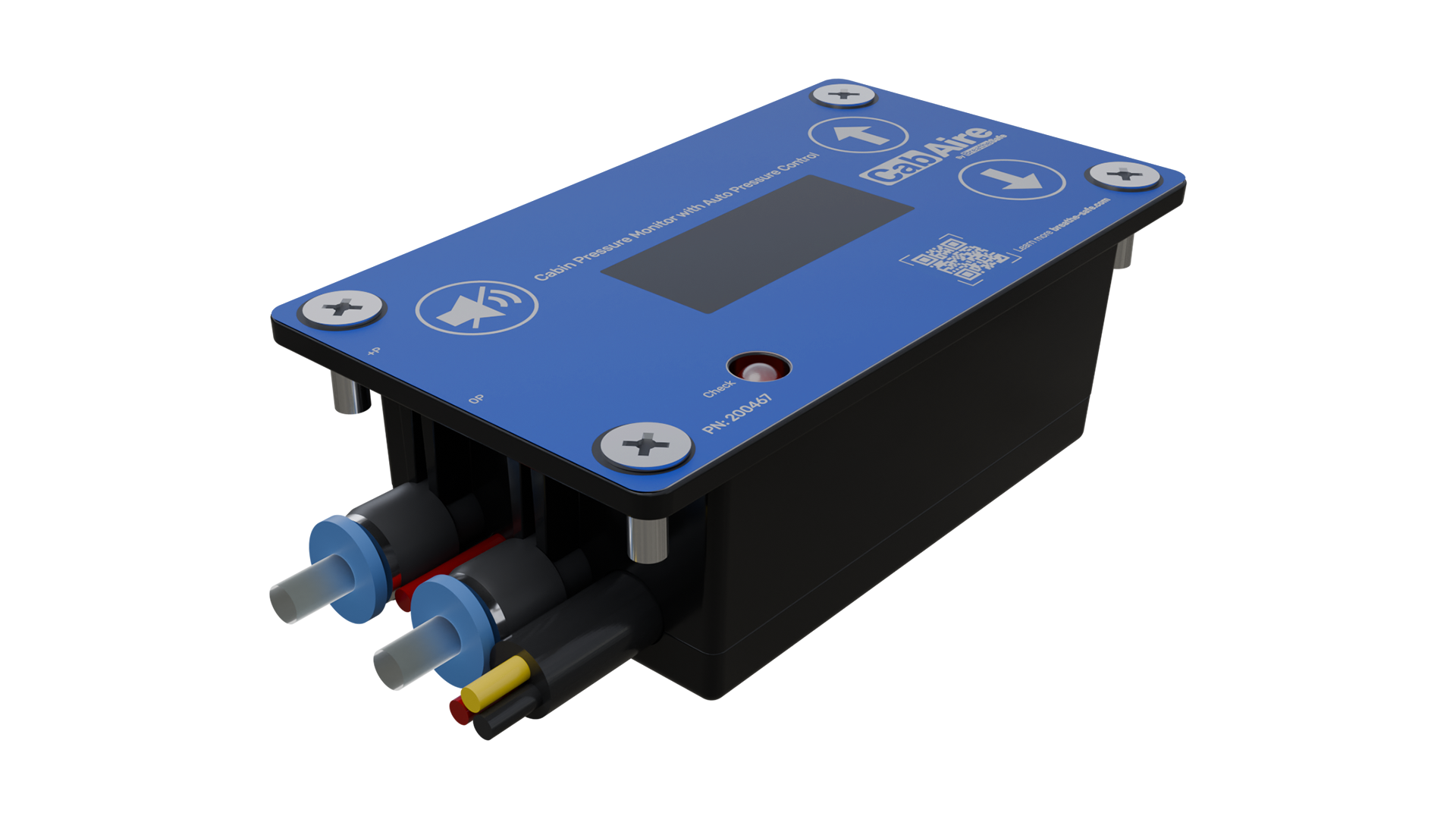
2024
11/09
Product Video – CabAire Pressure Monitor
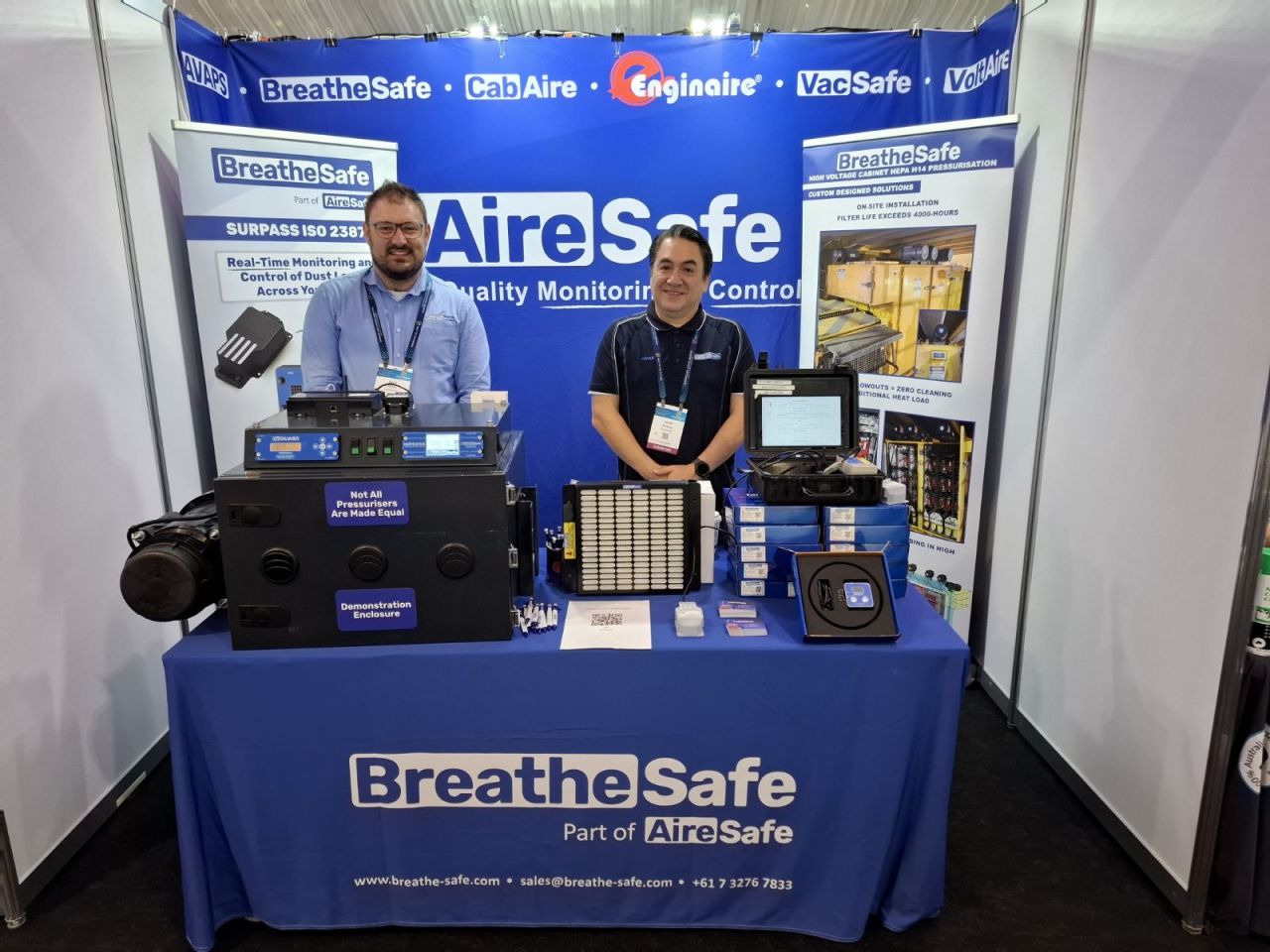
2024
21/08
Queensland Mining Industry Health & Safety Conference
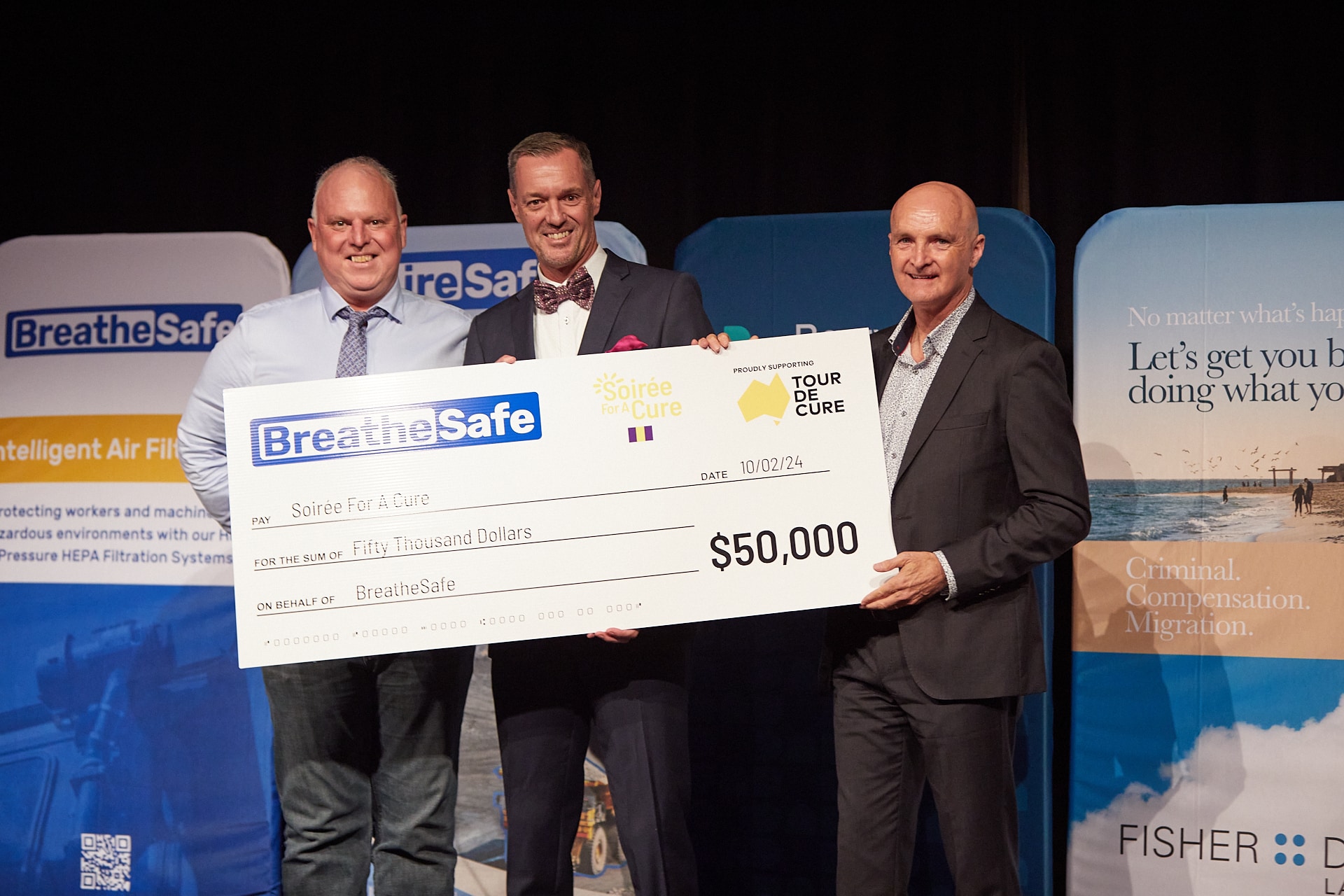
2024
12/02
BreatheSafe Cares – Soiree For A Cure
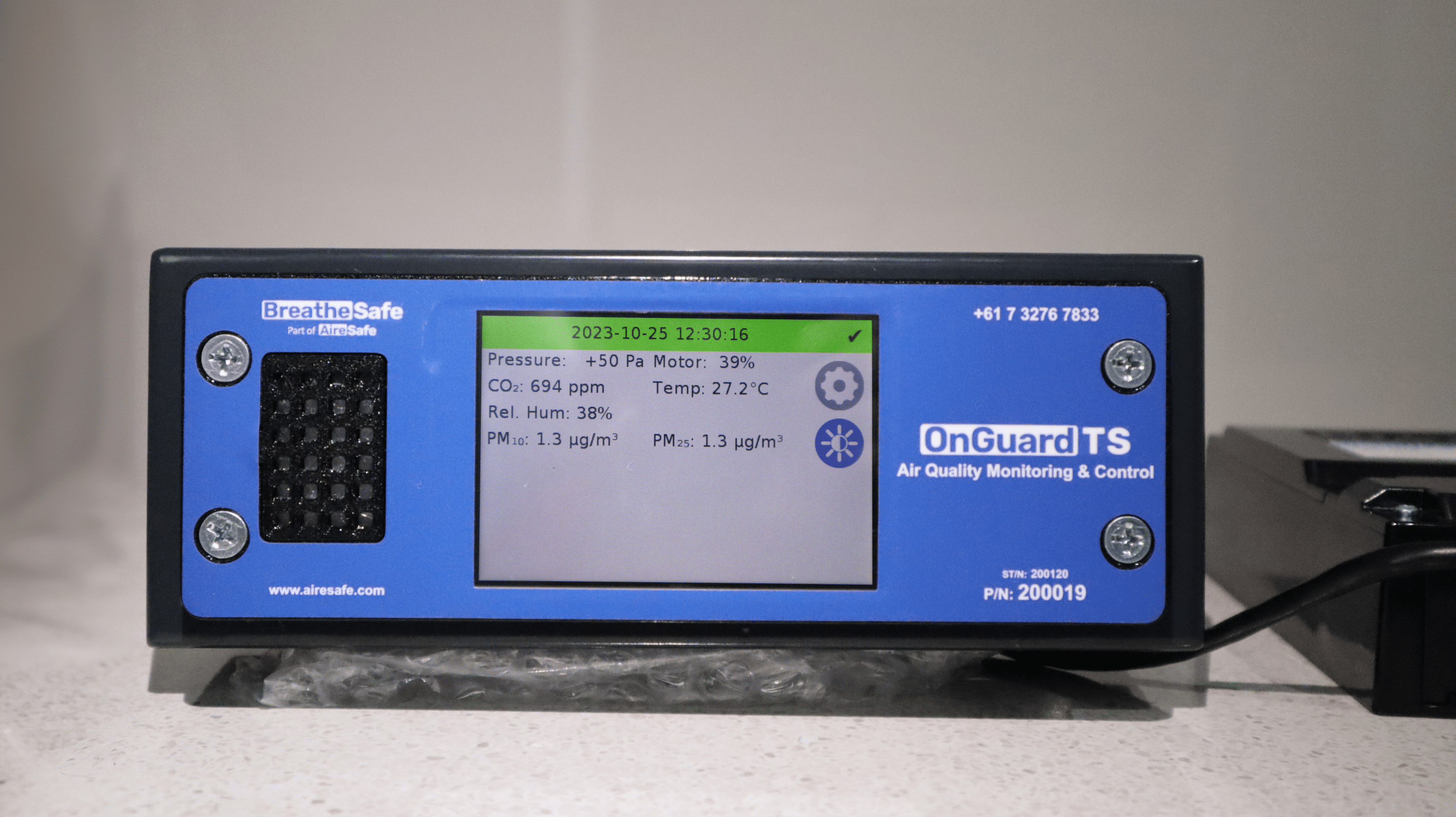
2024
07/02
The Ultimate Air Quality Management System – OnGuard
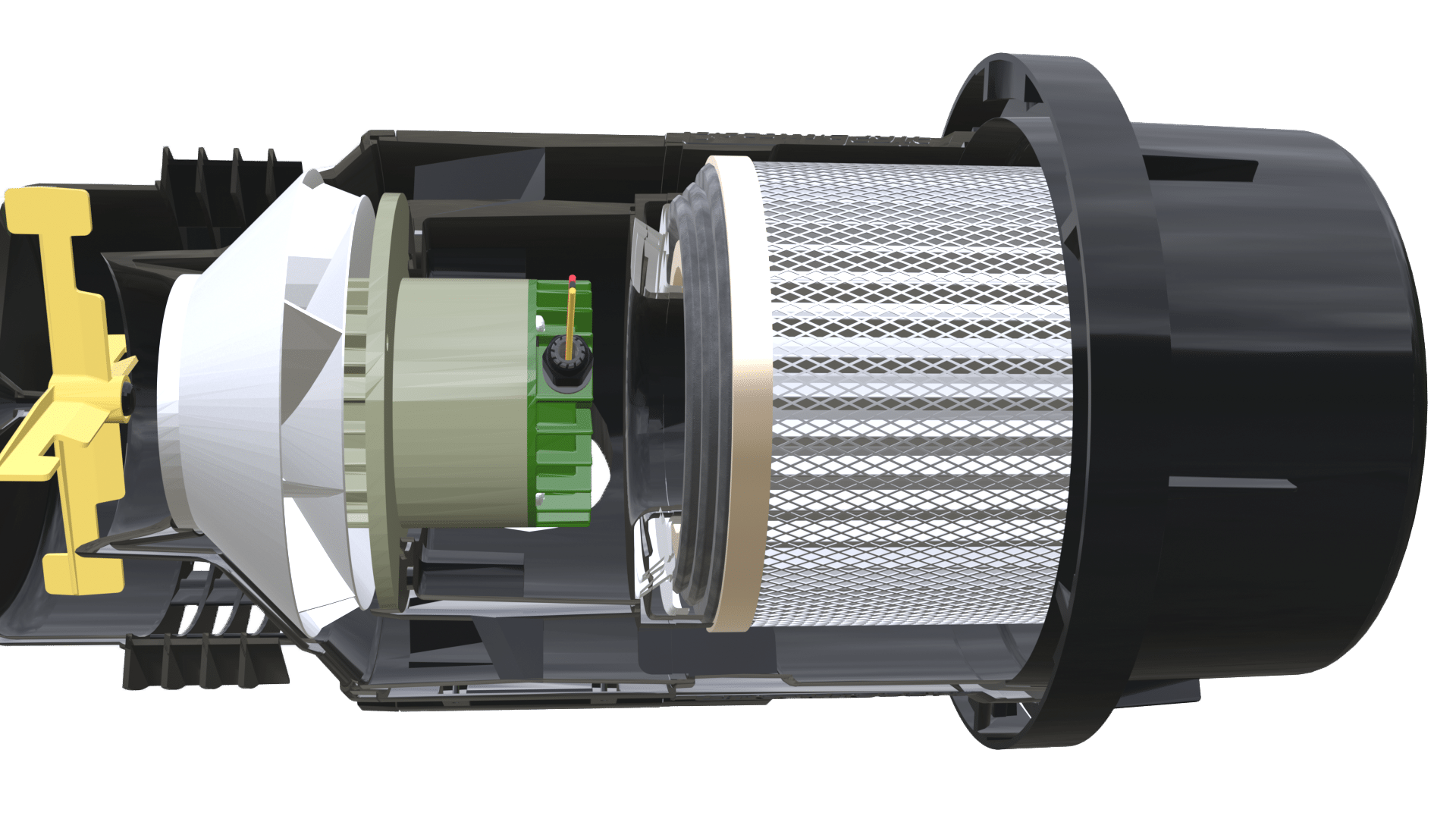
2023
01/11
Demo Video – Motor Replacement for TL Air Pressuriser
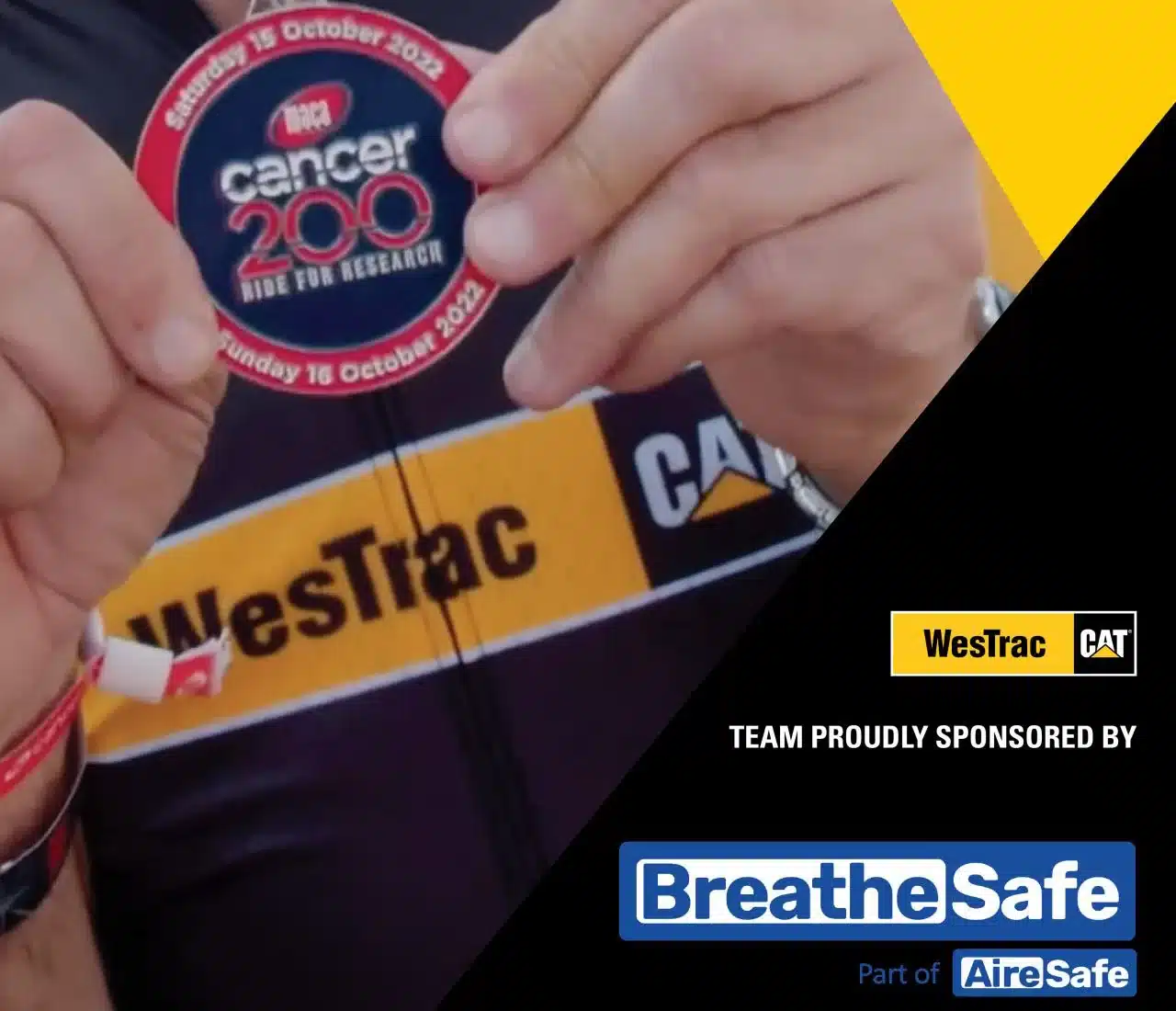
2023
15/10
BreatheSafe Cares – MACA Cancer 200 Ride
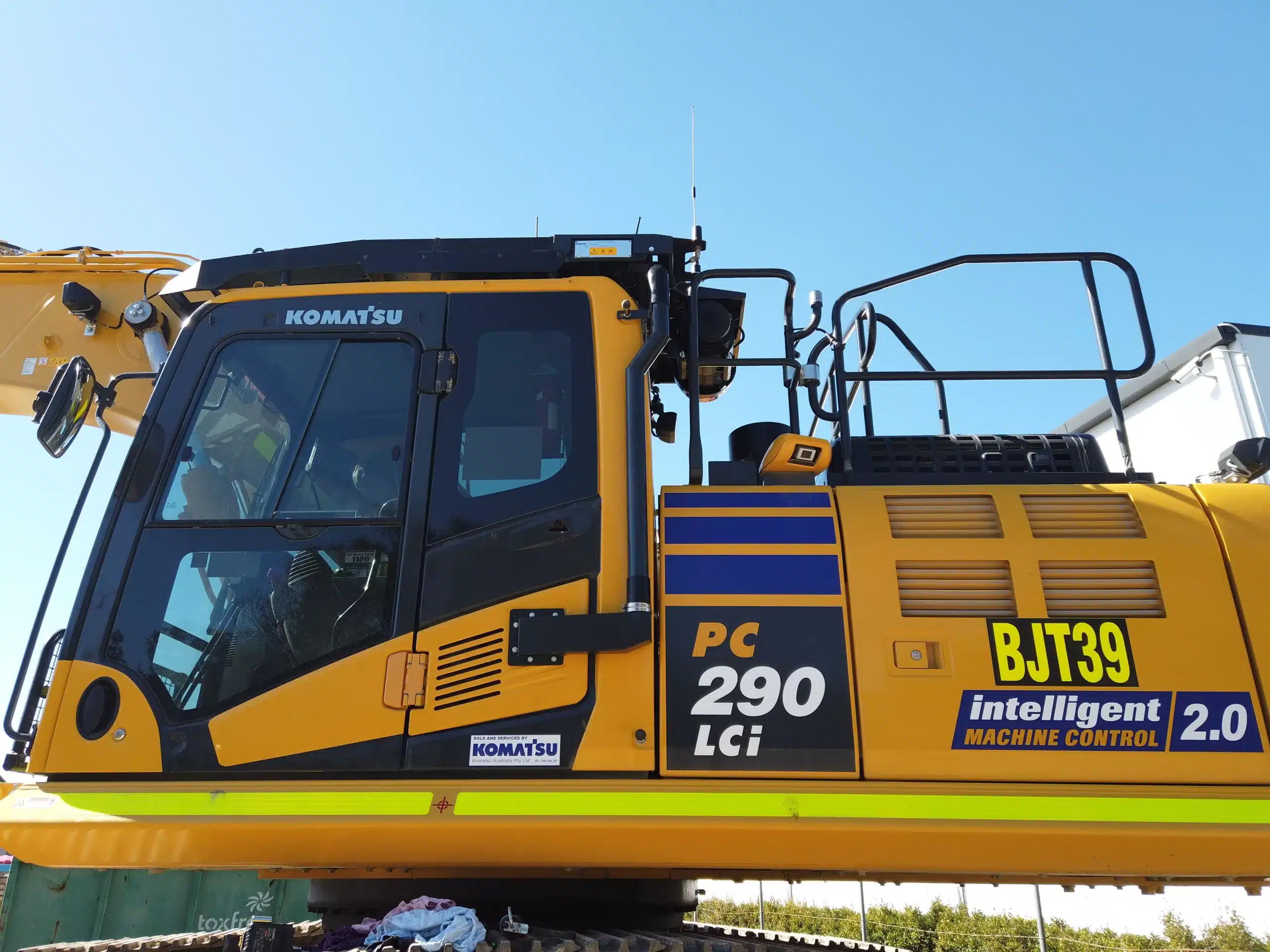
2023
04/10
System Installation – Komatsu Excavator PC290LCi-11
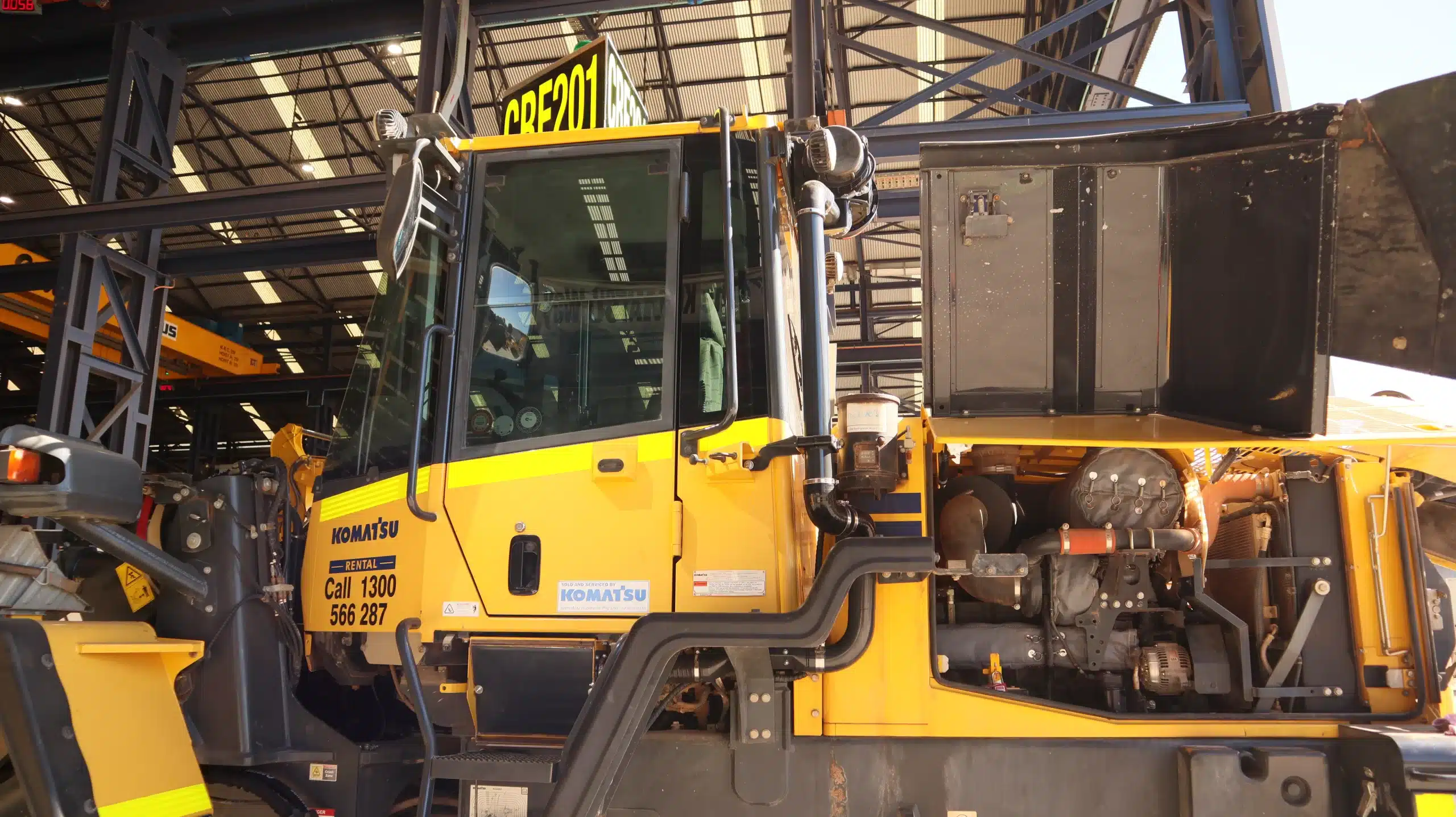
2023
15/08
System Installation – Komatsu Wheel Loader WA250PZ-6
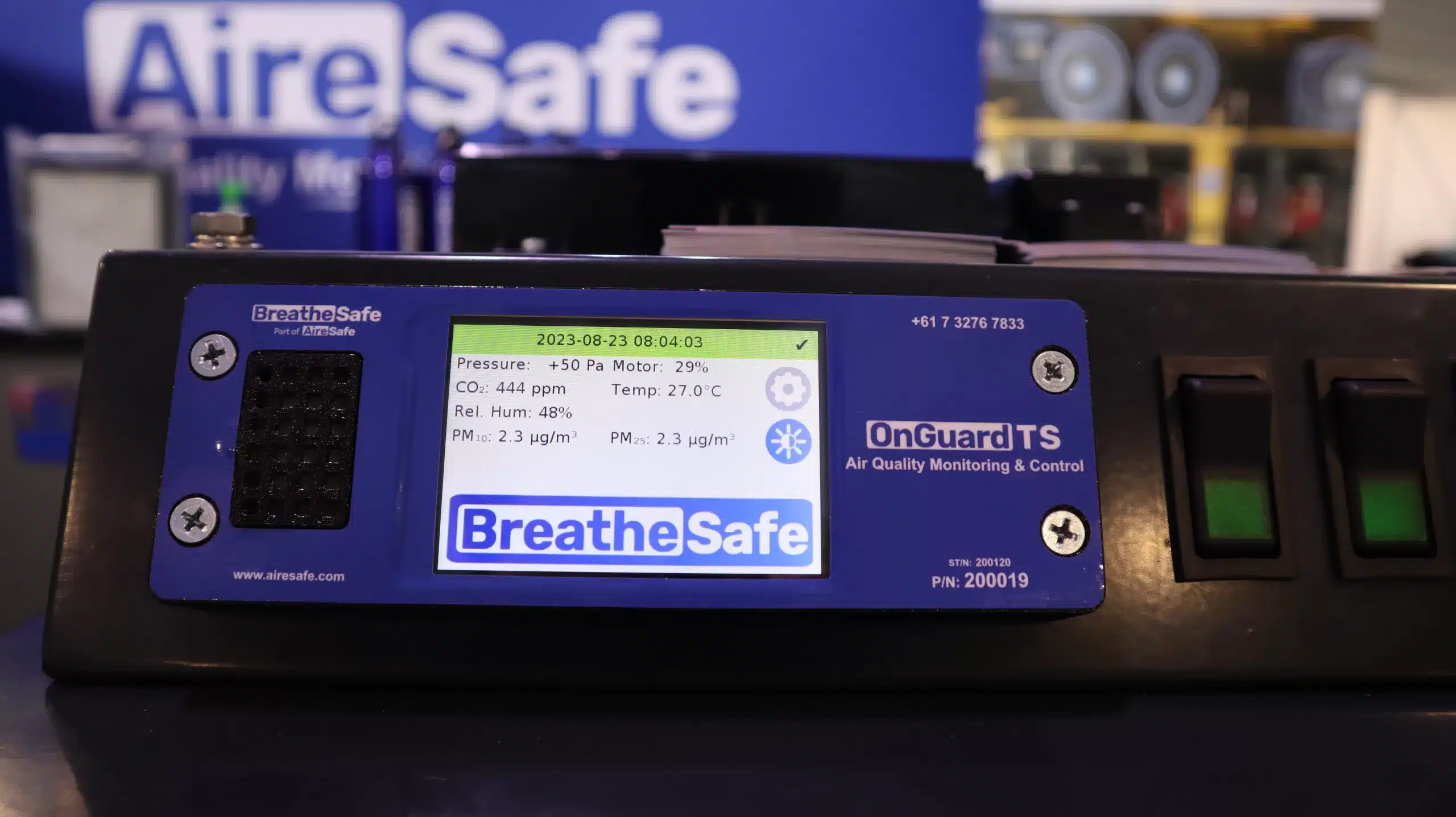
2023
13/07
Remote Air Quality Control by OnGuard Monitor & Controller
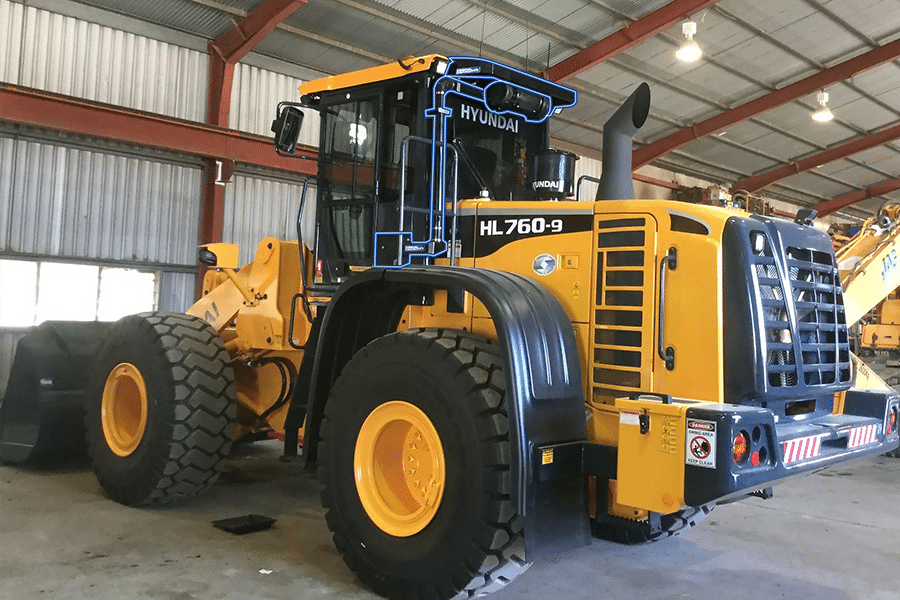
2023
13/07
Comply with ISO23875 – BreatheSafe Cabin Air Purification
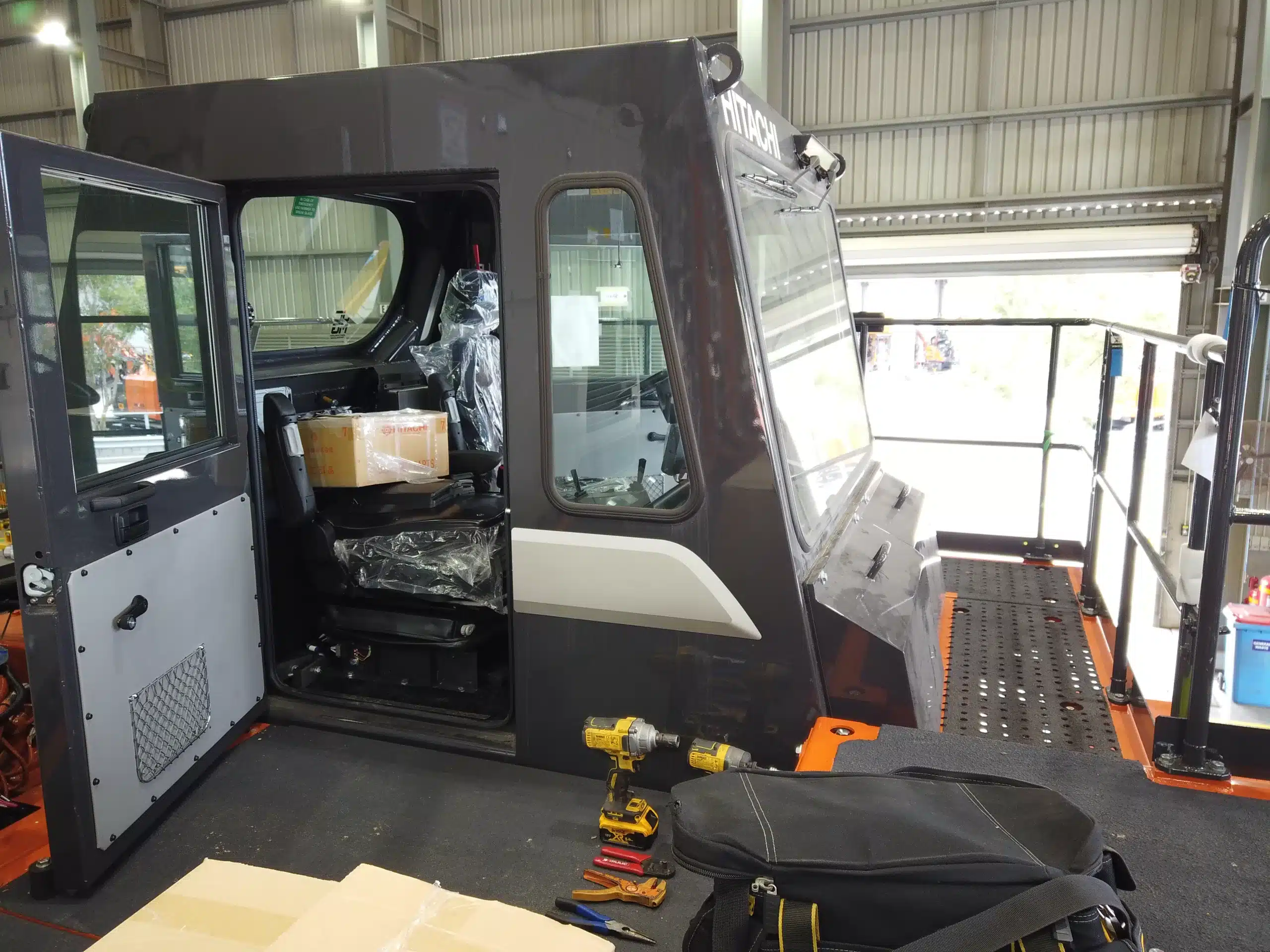
2022
01/11
System Installation – Hitachi Haul Truck EH3500
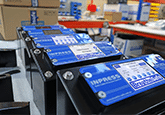
2022
14/06
Industry Standards and Regulations
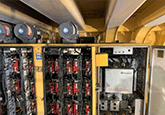
2021
20/12
Meandu Trial Cabinet Dust Prevention
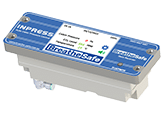
2021
06/10
Meet and Exceed ISO23875 with INPRESS TS Controller
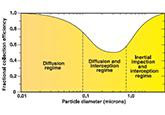
2021
20/09
Five Common Misconceptions about Air Filters
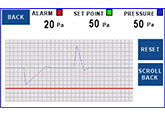
2021
31/08
Data Monitoring: The Key to Success in Minimising Exposure to Dust
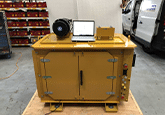
2021
26/07
BHP Autonomous Cabinet Field Trial
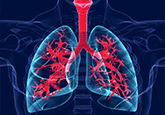
2021
06/06
RPME is the BEST PRACTICE to Stop Respirable Dust
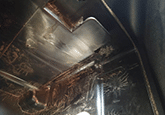
2021
06/06
OEM Cabin Filters Were Not Designed to Stop Respirable Dust
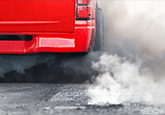