BreatheSafe consulted with Meandu Coal Mine concerning airborne mine dust in their high voltage cabinets. A High Pressure HEPA Filtration system was specifically designed and installed on a Komatsu 830E HV cabinet with four TL pressurisers.
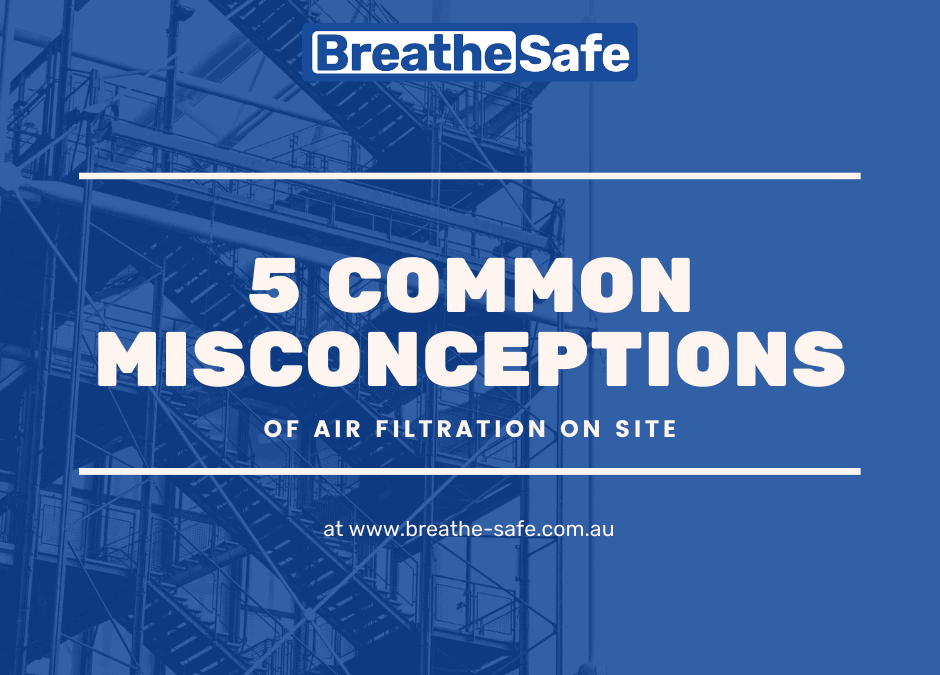
Five Common Misconceptions about Air Filters
Five Common Misconceptions About Air Filters
September 20, 2021
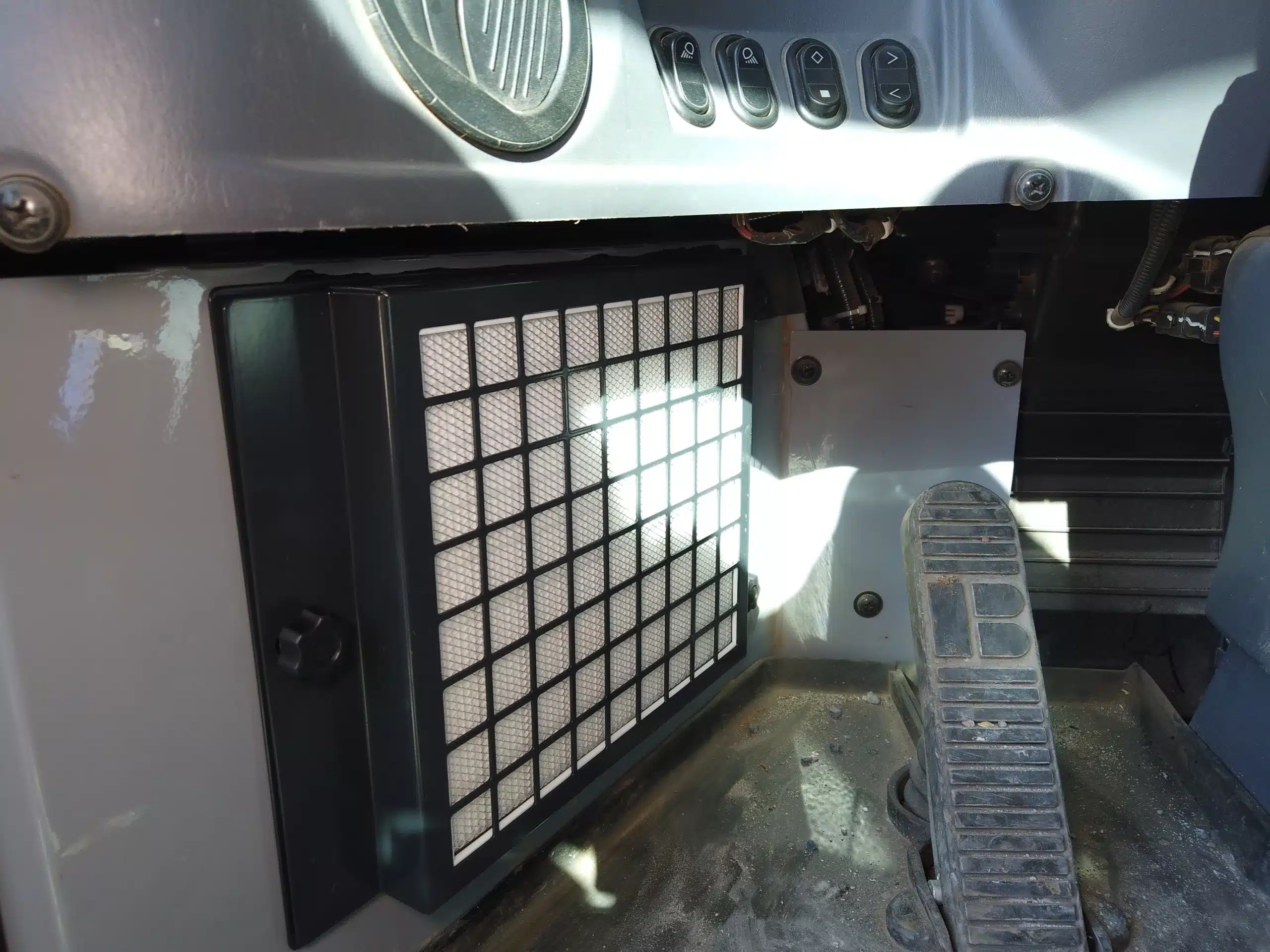
There’s lots of information out there about air filters, particularly in the time of COVID-19. But for industrial air filtration and pressurisation in hazardous environments, we find the same misconceptions popping up repeatedly.
1) Cabin pressure is enough to protect operators
Positive pressure does keep hazardous dust from entering into the cab through tiny openings. However, it doesn’t stop hazardous dust from entering the cabin. Ambient air is pumped into the cabin to create a positive pressure difference between inside and outside. This ambient air, however, still contains all of the harmful airborne particulates outside!
By filtering this fresh air, purified and clean air enters the cabin and blows into the operator breathing zone.
2) Air filters will restrict airflow in the vehicle
In traditionally designed pressurisers, the higher the efficiency class of your filter, the less airflow entered the cabin. This is why many brands market MERV-16 or EPA filters as the optimal combination between airflow, price and filtration efficiency.
However, BreatheSafe High Pressure Filtration systems can maintain appropriate airflow, even with higher classes of filtration. As standard, we sell HEPA H14 filters in our pressure systems. We believe that filtration is a significant factor in protecting the enclosed area from hazardous dust. This airflow is capable because of the brushless motors and advanced intelligent motor power control of in-cabin pressure.
3) HEPA air filters are only 99.99% effective
HEPA classification works on its effectiveness in filtering particles at the Most Penetrating Particle Size (MPPS). Particles of approximately 0.3 μm – the MPPS – are the hardest to catch. The size at which the air filter has its lowest arrestance value and penetrates through filtration processes at the most common rate. For this reason, the European standard EN 1822 assesses the filtration performance of the filter by measuring the penetration of 0.3 μm sized particles. Much smaller nanoparticles are easier to catch.
Tests conducted by NASA showed that HEPA filters are highly effective in capturing up to 100% of nanoparticulate contaminants and larger particles greater than 0.3 μm. However, for particles around the MPPS, there is a tiny drop in filtration efficiency.
(Wikipedia)
According to EN 1822, a HEPA filter must remove at least 99.95% of particles sized 0.3 μm or larger. US government standards require a filter to remove 99.97% of particles sized 0.3 μm to qualify as HEPA.
That is why HEPA filters are actually more than 99.99% effective at removing hazardous particles from the air but are rated as so. These MMPS particles are still dangerous, which is why the higher the %, the better it is for your health.
4) Replace air filters when they look dirty
A common question we receive is, isn’t replacing filters expensive?
We’ve found that many customers are replacing their filters well before they are full. It is particularly worrying because the fuller a filter is, the more effective it is. Our INPRESS system includes automatic motor power control that increases when pressure within the cabin decreases. Cabin pressure decreases over time due to the filter filling up, and when the INPRESS sees it getting lower, it increases blower speed to maintain the pressure setpoint. In addition, the INPRESS will let you know when the filter is too full when the motor is going at excessive speeds. This extends filter life and prevents early changing, saving you money.
With motor control, it also blows through lower volumes of air to maintain that pressure, meaning less debris and the particulate matter goes through the filter, filling it up slower. We have introduced a new touch screen display that shows in real-time the capacity of our pressuriser, which means sites will know when to replace filters! That’s a cost-saving that can be multiplied by all the machines equipped with BreatheSafe systems.
5) An air filter will heat up the cabin
Traditional pressuriser designs run their motors at 100% consistently to maintain airflow, resulting in a noisy, hot machine and atmosphere. An uncomfortable operator enclosure can result in untrained operators winding down windows for fresh air, letting all the hazardous particles inside.
However, we design BreatheSafe High Pressure Air Filtration systems to blend with the machines pre-existing airconditioning system, so the fresh, clean air is cooled before entering the cabin. Beyond that, our motors run with minimal power and still provide substantial airflow, maintaining a comfortable enclosure in even the hottest environments.
How many of these misconceptions did you believe? Let us know!
Related Articles
Meandu Trial HV Cabinet Dust Prevention
Meet and exceed ISO23875 with INPRESS TS Controller
The new ISO 23875 standard places a greater emphasis on the air quality inside the operator cabin...
Safe Work Month 2021
Safe Work Month 21 starts today with the theme think safe, work safe, be safe. As a...